You wouldn’t fuel your car with just any oil, would you? Well, the same principle applies to air compressors. For your air compressor to keep running smoothly and efficiently, using the right type of oil is critical. Just like any other machine with moving components, air compressors need regular lubrication to work well, reduce energy consumption, and avoid breakdowns.
That’s why today, we’re going to take a look at the kinds of oil you should use for your air compressor, how to change the oil, and some important tips to keep your air compressor in tip-top condition. Let’s dive right in.

Why Should You Use The Right Kind of Oil For Your Air Compressor?
Air compressors work by compressing air using pistons or rotary screws. Internal components are affected by friction and heat during the compression process, which can cause wear and tear.
Compressor oil’s primary function is cooling. Think of it as your system’s personal AC, dissipating heat generated from the compression process. If left unchecked that heat can cause some serious damage to your air compressor, significantly impacting its longevity.
But that’s not all. Compressor oil also seals the compression chambers and serves as a lubricant for the rotors. It seals the compression chamber by flowing in between the screw elements, sealing the compressed air space. Air compressor oils also have rust and corrosion inhibitors, which help protect the compressor’s components from, you guessed it: rust and corrosion.
Using the right kind of oil is critical for the performance and longevity of the air compressor. Using the wrong oil or a lack of upkeep can result in higher energy consumption, decreased performance, and even damage to the compressor's internal components.
Types of Oil for Air Compressors
You might be wondering, what kind of oil does an air compressor take? To answer your question, the type of oil you should use in your air compressor is determined by its design and intended use.
Air compressors use three types of oil: standard oil, which is basically petroleum or mineral oil, synthetic oil, and semi-synthetic oil. Let’s take a closer look at each of them and what they bring to the table.
1 - Standard Oil
Standard oil or mineral oil, also known as petroleum-based oil, is the most common type of oil used in air compressors. It is affordable and widely available. This oil is suitable for the majority of conventional air compressors used in home workshops, small companies, and light-duty applications.
Standard oil is generally cheaper than synthetic oil, which makes it a more cost-effective option for most people. But as we’ll discuss later, being a cheaper alternative shouldn’t make it your preferred option. Since it is more volatile than synthetic oil, mineral oil is more likely to evaporate and get depleted quickly.

On the flip side, it has a higher oil carry-over, which means it is able to enter the compressed air network despite the oil filter and oil separator downstream. Standard oils are also substantially more reactive than synthetic oils. Since the carbon chains aren’t completely saturated with hydrogen, the oil reacts quickly with other chemicals and can create clumps.
Standard oil also needs to be changed much more regularly than synthetic oil, and it also shows its flaws when it comes to performing under extreme temperatures or under heavy loads. Standard oil is typically used in air compressors that are used sporadically, or by DIY enthusiasts with less demanding applications.
Standard/Mineral oil is best suited for:
Light Industrial Use: Mineral oil can be a viable choice in some small-scale production environments if the air compressor is used periodically and for light-duty jobs. These could entail packaging, light assembly, or powering basic pneumatic equipment.
Home Workshops: As we mentioned earlier, mineral oil is a cost-effective option for amateurs and DIY enthusiasts with small air compressors used for infrequent chores such as filling tires, powering airbrushes, or running small pneumatic tools. It has good lubricating qualities for these low-demand tasks.
However, there are some situations in which mineral oil may not be the ideal option:
High-Temperature Environments: Mineral oil may degrade faster and need more frequent oil changes in industries or applications where the air compressor operates at high temperatures, such as continuous manufacturing processes. Synthetic oil, for example, is more appropriate in metalworking facilities with air compressors running at full capacity for extended periods of time.
High-Pressure and Heavy-Duty Compressors: Synthetic oils are often selected for air compressors utilized in heavy industries, building sites, or large-scale manufacturing where the machines are subjected to tremendous loads and pressure. Synthetic oils are an excellent choice for such demanding applications due to their performance and longevity.
2 - Synthetic Oil

As its name suggests, synthetic oil is made with a synthetic base. It was basically designed to be better than standard oil in every way possible, and as you’ll see, it pretty much is. Synthetic oil offers better heat protection, lubrication, and service life than standard oil. The need for frequent oil changes is also eliminated, owing to the fact that synthetic oils run nearly two times longer than standard oils. The longer oil change intervals are caused by its higher resistance to oxidation.
Additionally, synthetic oil may improve compressor efficiency and minimize energy usage. Although it is typically more expensive than mineral oil, in some cases the benefits make it worth its higher price tag.
Synthetic oil works best for prolonged or intense use, as well as extremely hot and low-temperature conditions. But that’s not all, unlike standard oil, synthetic oil doesn’t have any sulfur or additives, which aids in reducing valve buildup. It's also a suitable choice for applications that require longer maintenance intervals and less wear, as well as those that prioritize energy efficiency.
Some areas where synthetic oil shines are:
Heavy-Duty Industrial Compressors: Air compressors play an important role in powering heavy machinery and production lines in large factories, construction sites, and heavy industries. Synthetic oils can endure the harsh conditions found in these environments, such as high temperatures and pressure, without degrading.
Critical and high-value operations: Synthetic oils are preferred in industries where even a brief downtime can result in substantial losses, such as the pharmaceutical or semiconductor industries, to reduce the chance of compressor failure and production disruptions.
Continuous Operations: Synthetic oils thrive in applications that demand air compressors to run continuously for extended periods of time. It can considerably prolong oil change intervals and reduce maintenance downtime in facilities where air compressors are critical for round-the-clock manufacturing or processing.
However, while synthetic oils have many benefits, they may not be practical or cost-effective in some situations:
Cost Considerations: In general, synthetic oils are more expensive than mineral oils. The additional cost of synthetic oil may not be justified for small-scale applications or sporadic air compressor use.
Manufacturer's Recommendations: Some air compressor manufacturers may recommend using mineral oil for specific models, and using synthetic oil may void the warranty. Always consult the user manual or contact the manufacturer for recommendations on the best oil type for your individual air compressor.
3 - Semi-Synthetic Oil

If you haven’t connected the dots by now, semi-synthetic oil is a blend of mineral oil and synthetic oil. It combines the benefits of both types while mitigating some of their disadvantages. Here are some examples of where semi-synthetic oil can be useful:
Moderate to Heavy-Duty Applications: Semi-synthetic oil can find a balance between performance and cost in workshops or businesses with air compressors ranging from light-duty to heavy-duty operation. It provides better lubrication and protection than mineral oil, making it appropriate for more demanding jobs while remaining less expensive than full synthetic oil.
Temperature Fluctuations: The stability of semi-synthetic oil can be useful for air compressors working in conditions where temperatures vary dramatically. When compared to mineral oil, it has a higher resilience to break down under different heat conditions.
Which Oil Should I Use for My Air Compressor?
To determine the best oil for your air compressor, first and foremost, you should check your air compressor’s handbook and warranty. Always use the lubricant recommended by your air compressor's manufacturer for your individual make and model. Use a lubricant stock that is appropriate for your air compressor and the conditions under which it will work.
In addition to the base material, the lubricant weight, or viscosity, must be considered. Most air compressors require a non-detergent oil of 20 or 30 weight. A 20-weight is normally advised for colder regions, and a 30-weight is typically recommended for warmer environments.
Always use the suggested oil type and viscosity for your air compressor model, climate circumstances, and usage patterns when deciding between air compressor oil types. Ultimately, the decision between standard and synthetic oil will be determined by the specific needs of your budget, application, and operating environment.
How to Change Air Compressor Oil?
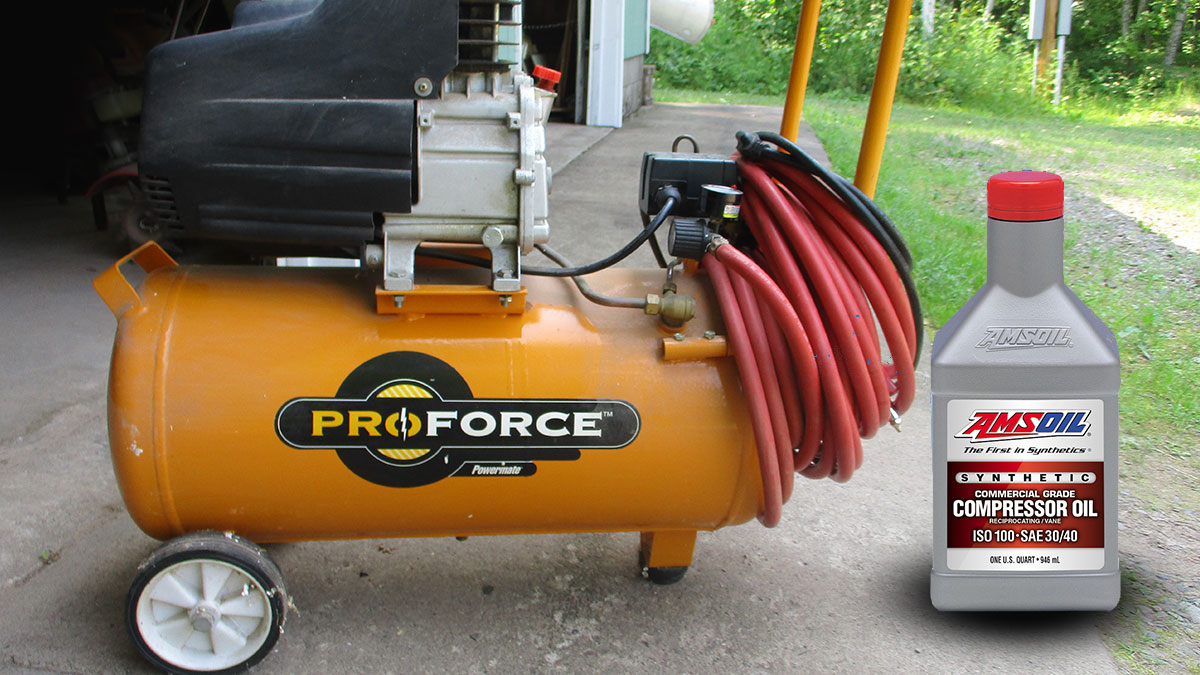
Regardless of operational conditions or hours of operation, compressor oil has to be replaced at least once a year. This is due to the fact that oil degrades over time and no longer provides adequate lubrication.
Most of the time, oil will need to be replaced more regularly. If the oil becomes contaminated or dirty, it should be flushed and replaced with new oil. Thick or opaque oil is a sign that your oil needs to be replaced. Some signs that your oil needs to be changed include discoloration, visible gritty particles, and an unpleasant odor.
Here's a step-by-step guide to changing the oil:
Safety First: Always turn off the air compressor and unplug it from the power source before beginning any maintenance. Allow the compressor to cool down before beginning any operation.
Drain the Old Oil: Identify the compressor's oil drain plug or valve. Place a container or oil pan beneath it to collect the used oil. Carefully remove the drain stopper and let the oil drain completely. Make sure to properly dispose of the old oil in accordance with your local environmental regulations.
Replace the Oil Filter (if necessary): Some air compressors have an oil filter. Replace it during the oil change if yours has one. A clean oil filter helps in oil circulation and filtration.
Add the New Oil: Follow the manufacturer's instructions for the proper oil type and viscosity. Pour the new oil cautiously into the compressor to avoid leaks. If necessary, you can use a funnel. Take care not to overfill the compressor. Check the oil level with the dipstick and make any necessary adjustments.
Check for Leaks: After adding new oil, look for any leaks near the oil drain cap and other connections. Repair any leaks before restarting the compressor.
And there you have it! Remember, choosing the right oil will definitely have a visible impact on your air compressor, and proper maintenance will keep it running like the smooth criminal it was supposed to be.