Have you ever found yourself scratching your head in frustration due to a defective air compressor? Well, you're not alone. Air compressors are amazing tools, but like all machines, they can throw us a few curveballs.
If you’re a DIY home improvement enthusiast or an experienced contractor earning a living with your tools, this one is for you. Having a reliable air compressor is a necessity.
That's why today, we'll walk you through how to troubleshoot your air compressor and use practical solutions to get it running smoothly again.

Common Air Compressor Problems
Problem 1: The Air Compressor Will Not Start
If your air compressor just won’t start, there could be a few reasons why:
No electrical power
Failure to start could also be the result of overlooked power connections, such as a disconnected power cord or a power switch that has been off. Just make sure you check the power button and switch before proceeding. If necessary, breakers should also be checked.
Low Oil Level
If the compressor’s oil level is too low, there is a good chance that your compressor won’t start. Try checking the oil level and replacing the oil if necessary.
Pressure Switch
The pressure switch is in charge of turning on and off the compressor at particular pressure levels. Verify that the pressure switch is set to the proper pressure range. If it isn’t, make the necessary adjustments. If it is, but the compressor still won't start, the pressure switch may need to be replaced. Always remember to unplug any electrical components before interacting with them.
Cut-In Pressure Setting
Your compressor won't start if there is a lack of sufficient air pressure in relation to the cut-in pressure. Adjust the cut-in pressure settings and see if the compressor starts. If it still won’t start, you might want to swap out the pressure switch for one that has a lower cut-in PSI.
Problem 2: The Air Compressor Won't Stop Running
If your air compressor refuses to take a breather and continues to run even when not in use, you may be dealing with a variety of issues.
Leaking Pressure Valve
The pressure release valve keeps compressed air from returning to the pump after it has been compressed. A leak here can cause the compressor to run continuously.
Locate the valve and inspect it for leaks. If you see any air escaping, cut the power and replace it. Also, inspect the air hose and connectors for leakage. A leaking pressure release valve can be pretty dangerous, so the sooner you address this, the better.
Faulty Power Switch
If you’re dealing with a faulty power switch, there’s a chance that your compressor won’t send a switch-off signal to internal controls. Installing a new switch should address the problem in this case.
Defective Pressure Switch
A functional pressure switch sends a signal to the compressor’s internal controls to stop running once the tank pressure gets to the cut-off point. If your pressure switch is faulty, replacing it should solve the issue.
Problem 3: Low Air Pressure

Is your pneumatic tool losing its oomph? If the air pressure appears to be lower than usual, there are a few culprits that could be causing the problem. If you're experiencing pressure-related issues, the first step is to find out whether you're dealing with a compressor or distribution line problem.
Compressor Problems
Incorrect Pressure Settings
The compressor may fail to maintain the necessary pressure if its pressure settings are incorrect. The root cause could be a faulty pressure switch or indicator, or it may just need some adjustment.
Compressor Leaks
Compressor leaks are a major cause of pressure irregularities. They could be found in the seals, fittings, valves, cooling system, or a connected air tank of the compressor.
Worn Air-intake Pump
The compressor's air intake pump, which is responsible for pressurizing the air, might wear down over time. In this case, it is no longer capable of exerting as much pressure as it once did.
Distribution Line Issues
If the air compressor is producing the right amount of PSI but there is insufficient pressure at the point of use; you're dealing with a distribution line issue. Some reasons why you may be experiencing this are:
Air leaks in distribution lines/valves
Leaks can arise in different areas, including pipelines, hoses, fittings, and valves. Over time, even small leaks can amount to significant air loss and energy waste. Pinhole leaks can pop up anywhere, especially with older distribution systems.
Distribution line leaks mainly occur in the condensate drains, valves, joints, and links, seals and gaskets, and hoses and quick connections. Hoses and quick connections demand special attention since they are the biggest cause of pressure loss in any distribution system.
Friction
The friction in pipes and hoses significantly affects the pressure loss in a compressed air system. Compressed air moving through the pipes and hoses faces friction loss, which results in a loss of pressure. Some elements that affect the degree of friction loss are the length, roughness, and diameter of the pipes and hoses, the bends, fittings and valves, and the airflow rate.
Lowering the length of runs, and limiting sharp turns in the distribution system will reduce pressure loss due to friction. Replacing hoses and couplers with permanent metal tubes wherever you can also reduce friction loss.
Small Hoses
Hoses are generally rougher and smaller in diameter than metal piping for compressed air. Using large pipes has no impact on the compressor's efficiency, but using small pipes can result in a loss of pressure across the distribution system. It is crucial to use appropriately sized piping to mitigate pressure drops and enhance your system's efficiency.
Problem 4: Excessive Noise
Air compressors aren't known for their quiet nature, but if yours suddenly sounds like a jet engine ready for takeoff, something is definitely wrong. Excessive noise could be caused by:
Worn-out Bearings or Loose Components
Tighten any loose bolts and nuts and, if necessary, oil the bearings to resolve this issue.
Mounting Issues
A compressor that is not properly mounted on its mount can also make a lot of noise while running. To address that, tighten the fasteners or insert vibration cushions. If the noise persists, it could be a sign of a more serious mechanical problem that needs expert assistance.
Problem 5: Compressor Vibrating
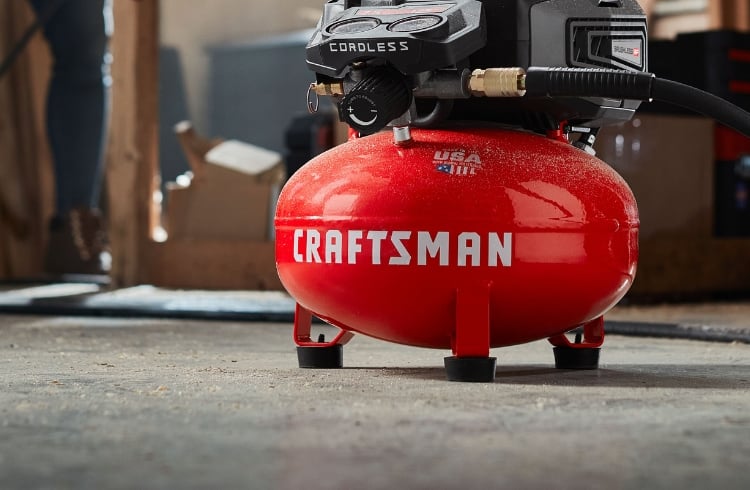
Compressor vibration is a relatively common problem, but it still needs your attention. Let's check out the possible causes of why your compressor is shaking things up and find some remedies to restore peace to your office.
Loose Mounting Bolts
When the mounting bolts are loose, your compressor is bound to vibrate all over the place. The solution? Grab your wrench and tighten those bolts up. It's an easy fix that can make a huge impact.
Incorrect Compressor Mounting
Sometimes, your compressor might not be standing on solid ground, causing it to wobble and vibrate. To fix this, you'll need to level the compressor properly, ensuring that all its feet are firmly placed on the ground before finally tightening the bolts.
Misaligned Pulley and Flywheel
If your compressor's pulley and flywheel are out of rhythm, it might set off a real vibration party. The solution is to get them back in alignment.
Loose Belts
Loose belts can contribute to compressor vibration. To settle things down, tighten those belts up. A well-tensioned belt maintains the rhythm smoothly.
Bent Crankshaft
Sometimes, the heart of the compressor, the crankshaft, might get bent, generating erratic vibrations. The fix here is a bit more complicated. You'll need to repair the crankshaft to get rid of the compressor's vibrations.
Problem 6: Overheating
One of the most frustrating issues you might encounter with your air compressor is overheating. If your machine starts ‘running a fever’, there could be several causes behind this problem. Let's check out what might be causing your air compressor to overheat and go through some solutions to cool things down.
Poor Lubrication
Your compressor needs to be well-oiled to perform efficiently. Poor or inadequate lubrication can cause higher friction and heat build-up. Inspect the oil system regularly to ensure that it is cycling oil appropriately. If the oil level is low, top it up; if the oil is dirty or deteriorated, it's time for an oil change. Bad Ventilation
If your compressor runs in a poorly ventilated area, it could struggle to dissipate the heat it produces. Inadequate ventilation might lead to the machine overheating. To solve this, make sure the compressor room is well-ventilated.
High External Temperatures
Running an air compressor in a hot environment can overwork the cooling system, making it more difficult for the unit to stay within recommended temperature limits. Make sure that the ambient temperatures aren’t too high. If necessary, consider adding fans or cooling systems.
Clogged Filters and Hoses
Filters and hoses clogged with dirt, debris, or pollutants can interfere with the compressor’s airflow and heat dissipation, resulting in overheating. Check intake filters, inline filters, pipes, and hoses for blockages regularly. Remove any obstacles and replace any dirty or clogged filters.
Cooling System Issues
Any problem with the air compressor's cooling system, such as faulty fans, blocked aftercoolers (for air-cooled systems), or low water or coolant levels (for liquid-cooled systems), might lead to overheating. Check out the cooling system, fans, and aftercoolers regularly. To ensure proper operation, clean them. Make sure that fans are working in air-cooled systems, and that water or coolant levels are closely monitored in liquid-cooled systems.
Over-Cycling
Extending the air compressor's duty cycle (the ratio of running time to rest time) can produce excessive wear and tear, resulting in overheating. To get ahead of this, ensure that you are operating the compressor within its recommended duty cycle. Excessive running without enough downtime can result in overheating.
Problem 7: Excessive Power Consumption
Are your power bills suddenly skyrocketing with no valid explanation? Your air compressor might be munching more energy than it should. If your air compressor acts like it's training for a powerlifting competition, there are a few reasons that could be contributing to this excessive power consumption:
Lack of Maintenance
Just as your car needs its oil changed and tires rotated, so does your air compressor. Failure to perform routine maintenance activities such as cleaning parts, replacing air and oil filters, and draining condensation might cause your compressor to work harder and consume more electricity. Change the oil, clean or replace the air and oil filters, and look for and repair any hidden leaks. A well-maintained compressor is an efficient compressor.
Air Leaks
When there are air leaks in your system, your compressor needs to work harder to keep up with the demand. Those leaks are stealing the compressed air you're paying for, forcing your compressor to work harder and consume more power to compensate. Check for leaks regularly and fix them appropriately.
Operating at High Pressures
It’s common for us to believe that higher pressure equals better performance. But running your compressor at higher pressures than necessary doesn't make it stronger; it simply makes it a power-hungry beast. Always ensure that your compressor is only working as hard as it needs to. Change the pressure settings to meet the needs of your operations. This simple change can help you save a surprising amount of energy.
Aging or failing motor
If your air compressor's motor is showing signs of wear or is on the verge of failing, it will become less efficient. An inefficient motor consumes more energy. If your compressor is old and its motor isn't working efficiently, it's time to replace it. Newer compressor types, particularly Variable Speed Drive (VSD) air compressors, are energy-saving masters. They adapt their power consumption to your requirements, making them far more efficient.
Problem 8: Blowing Fuses
If your air compressor has a knack for blowing fuses, it could signify an underlying electrical issue. The last thing you want is to constantly replace fuses like they're going out of style. Let's look into the various causes behind this issue and some smart solutions to keep your compressor running without blowing a fuse.

Circuit Overload
Sometimes, your compressor could be sharing the circuit with other electricity guzzlers. The solution here is simple: make sure your air compressor has its own circuit, rated for its amperage.
Motor Problems
A failing motor might use more current than it should, resulting in fuse-blowing drama. Take a look at the motor for evidence of wear or corrosion; replacing it often saves your fuses.
Wiring Issues
Inside the compressor, the electrical wiring can sometimes misbehave, with damaged wires or faulty connections leading to blown fuses. Give the wiring a thorough inspection for damages and loose connections, and make any necessary repairs.
Overheating
We've already discussed how bad overheating can be for your compressor. If your unit is operating hot, it's like a pressure cooker, and that's never good for fuses. Ensure it works in a cool, well-ventilated place to keep the temperature in check.
Pressure Levels
Going over the rated PSI can be a fuse's worst nightmare. Stick to the correct pressure levels to avoid any electrical problems.
Problem 9: Excessive Oil Consumption
Excessive oil usage can be a troublesome situation. Let's explore the problem and learn some basic strategies to keep your compressor well-lubricated without breaking the bank.
Restricted Air Intake
A clogged or dirty air filter is a major cause of high oil consumption. The solution? Give that filter a good wash or replace it with a new one.
Oil Leaks
Leaky bolts or a worn-out gasket can transform your compressor into an oil puddle generator. To stop this slippery situation, tighten those bolts or replace the gasket. It's a simple adjustment that can help you save on oil consumption.
Worn Piston Rings
If your compressor's piston rings are worn, they can't do their job efficiently, resulting in excessive oil usage. The solution? Replace those tired rings, and your compressor will work better.
Wrong Oil Viscosity
Using the wrong oil viscosity is damaging to your compressor. To fix this, drain out the improper oil and refill it with the oil of the right viscosity.
Tilted Compressor
If your compressor is leaning to one side, it can impact oil circulation. To literally level the playing field, ensure sure your compressor is on even ground. Consider adding vibration pads to steady it, and you'll notice a more balanced oil consumption.
Problem 10: Oil in Discharge Air
Oily discharge can be a messy and annoying situation, so let's take a look at what could be causing this situation and how to sort it out.
Restricted Air Intake
When your compressor's air intake is choked up, it might lead to oil contamination in the discharge air. The solution: clean or replace the air filters. Think of it as a breath of fresh air for your machine.
Worn Piston Rings
Worn piston rings might let oil sneak through where it shouldn't be. To fix this, you'll want to replace those rings and bring back the tight seal they provide.
Excessive Oil in the Compressor
Sometimes, too much oil in the compressor might lead to oil making its way into the air. The solution is to drain the extra oil down to the recommended level stated on the sight gauge.
Wrong Oil Viscosity
Using the wrong oil viscosity is like attempting to fit a square peg into a round hole – it just won't work. Check the oil viscosity you're using and make sure it satisfies your compressor's specifications.
Piston Rings Installed Upside Down
Installing piston rings upside down can lead to oil leakage and pollution. To set things right, you'll need to repair the crankshaft and verify the rings are properly placed.
Problem 11: Compressor Suddenly Stops Working
Your compressor tapping out at the worst possible scenarios can be super annoying, to say the least. So let's shed some light on why your compressor can stop operating unexpectedly while offering some solutions to get it back in the game.
Bad Unloader Valve
Sometimes, the unloader valve, which plays a crucial part in the comp
ressor's performance, can go wild. When it's on the fritz, it can lead to unexpected shutdowns. All you need to do in this case is replace the unloader valve, and voila. You're back in business.
Loss of Power
Another sneaky culprit for abrupt compressor silence is a loss of power. The solution? Find a new, reliable power source, plug in your compressor, and watch it spring back to life.
Conclusion
By being aware of these common problems and their solutions, you'll be better prepared to troubleshoot and repair issues with your air compressor. Always remember that safety comes first, so make sure you turn off the power before working on any electrical components.
And there you have it; the ultimate air compressor troubleshooting guide. Air compressor issues may throw you for a loop, but with this guide, you're now prepared to face them head-on. Happy troubleshooting!